Alphabet soup.
When I added the 300mm Nikkor manual focus lens to my little D700 outfit, it was with the realization that this relatively little used optic did not justify spending a lot of money. So it was off to KEH.com where I picked up one marked ‘BGN’, meaning something between a beater and a dud. However, having purchased from this business in the past, I knew that they grade conservatively and earlier ‘BGN’ purchases had invariably resulted in fine gear with typical superficial markings from use. And so it turned out this time.
What I received, for less than one quarter the cost of the current f/4 AF optic, was a lens with pristine glass, a beyond smooth focus action and …. a wobbly telescoping hood. The trombone assembly for the latter is attached with three small screws and it was a matter of moments to remove it, disclosing that the cork friction strip inside was worn out. I took the easy way out and wrapped one-and-a-half turns of 3M Flue Tape around the inner cylinder and while the result is not pretty the wobble is no more. This is a thin, metallic tape with strong adhesive, and one $8 roll will do more lenses than you want to think about. I’ll give it a spray coat of high temperature matte black paint, of the kind used on car engines. It’s tough and will hide the tape nicely.
The lens focuses down to 8.2 feet (2.5m), which is like a 50mm lens at 16″. That’s close. It also focuses well past infinity, to compensate for warm days, owing to the expansion of the metal used in its construction.
Contrast is high, identical to that of the other two lenses, putting a well deserved lie to all the claptrap you read about ‘designed for digital’ lenses. This is a film era lens (around 1990s vintage) and works perfectly with the sensor in the D700. ‘Designed for Digital’ is yet another advertising hoax designed to separate the gullible from their money.
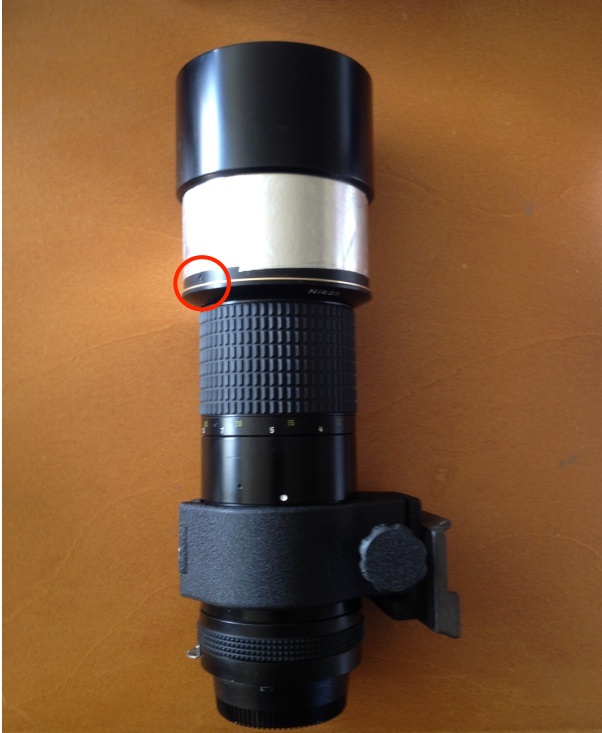
300mm MF Nikkor. Flue Tape prevents hood wobble.
Circle denotes one of the three trombone retaining screws.
If following moving action is your thing, this lens is not for you. Auto focus will make life much easier in that case. But my primary use is for architectural details, used as often as not with my Manfrotto monopod fitted with a QR release, so I’m in no hurry. The D700 has a focus confirmation light in the finder, with arrows showing which way to turn the focus collar if you are out of focus. This works really well but is very sensitive. In practice, other than at full aperture, I find that simply focusing on the screen works well, the high f/4.5 focusing aperture making images snap in and out of focus readily. The lens shows a hint of chromatic aberration wide open with high contrast subjects, but otherwise has no bad points. With the removable collar it weighs 2.2 lbs. and balances nicely with the heavy 2 lb. D700 body. I dialed it into the ‘Non-CPU lens’ menu on the D700 so the EXIF data correctly reports that a 300mm lens was used.
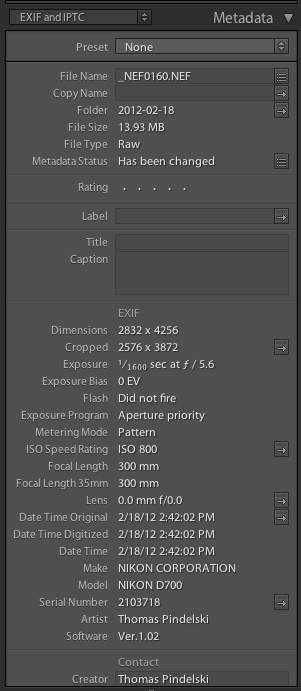
EXIF data in LR3.
Unfortunately, Lightroom sorts on the ‘Lens’ field when filtering images, so only the actual EXIF for an image will disclose that a 300mm lens was used. The ‘Focal Length’ and ‘Focal Length 35mm’ fields do not constitute searchable EXIF or IPTC data in LR, as far as I can tell. Good luck getting Adobe to fix that.
By virtue of the Internal Focusing design, operating the focus collar moves a selection of elements internally, not the whole lens barrel, so the length of the lens remains fixed and the action is butter smooth. Just a joy to use. I would describe the rendering of micro-detail as close to that of the very expensive 16-35mm and the bargain 85mm D designs, but not as good through f/5.6. At f/8, however, micro-contrast really kicks in and the definition equals that of the other two. A touch on the Clarity slider in LR3 mostly puts matters to right at f/4.5 and f/5.6, and I am finding that the 86/1.4/50/23 Sharpness settings in my import dialog in LR3 for the other two lenses works well.
The tripod collar, easily removed, is well designed, but not in the class of the one on the 400mm f/5.6 Canon L, adopting a threaded fastener in preference to the superior cam lock used by Canon. There is no Vibration Reduction, which keeps the weight down but that savings is offset by the need to carry a support if slow exposures are contemplated. With the collar removed I find the lens easy to handhold.
Wringing it out yesterday I made a few snaps in San Francisco in late sun, all at 800 ISO and mostly with a monopod. These are almost all straight from the RAW originals, with minimal post-processing, with the usual sharpening on import into LR3. The lens retains Aperture Priority (my choice) or Program exposure automation on the D700, with focus at full aperture:
To get a sense of what the lens can do in huge enlargements, here’s a snap at f/8, 1/50th second, ISO 800 with monopod:
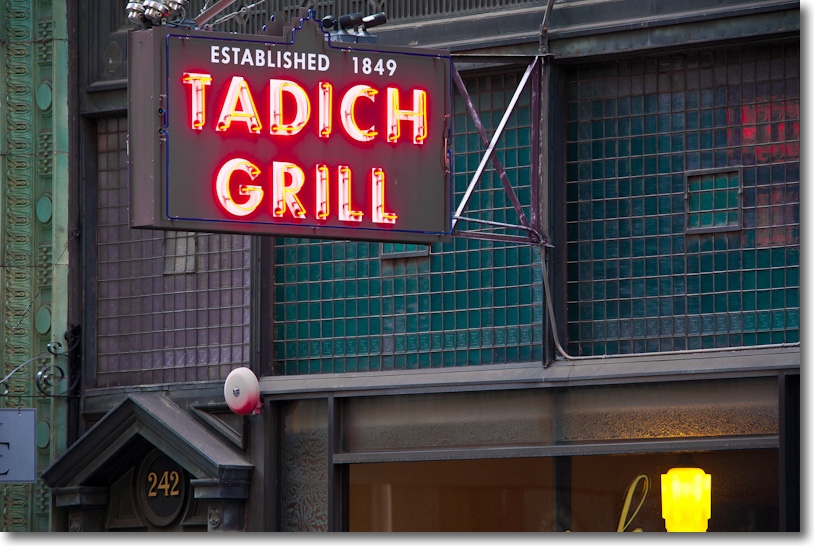
Here’s a section from the top left which would make a 40″ x 60″ print:

Not too shabby – notice the level of detail retained in even low contrast areas.
Adding a CPU:
While many lenses allow simple glueing of a CPU to the rear baffle, the baffle on this lens is too large in diameter to provide the required clearance for the CPU.
I therefore set to machining the baffle on my 300mm f/4.5 ED-IF Ai-S lens. The baffle is retained by three radial, countersunk Philips screws. The fourth, proud, slotted screw is for the stop down lever and is not touched.
After doing some measuring it turned out to be very simple. The full thickness of the baffle has to be removed and the depth of removal is conveniently denoted by a ridge on the baffle, visible once removed.
After marking the position of the CPU with a fine scribe, removing the three screws allows removal of the baffle. It shows traces of threadlocker so it would likely be smarter to use some local heat from a soldering iron on the screws first. I lucked out.
The lens’s tripod collar is removed in these pictures.
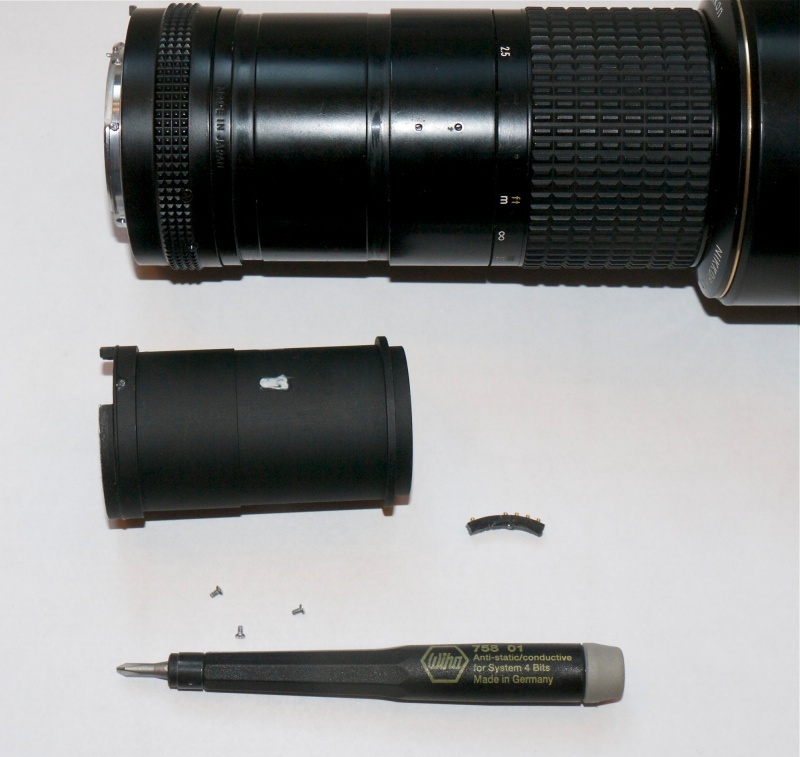
Three screws removed, the baffle can be slid out.
The thickness of the CPU body material is identical to that of the baffle’s wall, I used a Dremel cut-off wheel, a metal saw and a fine file to make the slot in the baffle. A milling machine would have been nicer! The CPU is circled in red below.
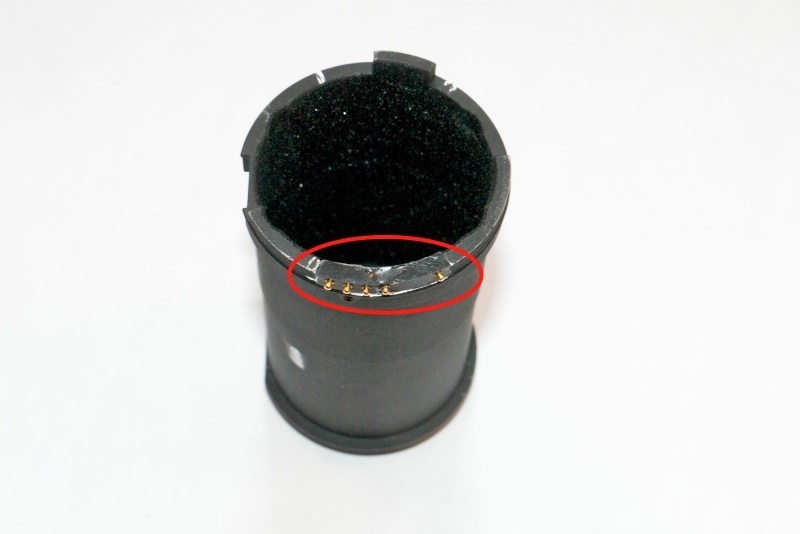
The CPU in place.
This lens’s baffle is 1.613″ in. outside diameter. The wall is 0.118″ thick, thus the inner diameter is (1.613 – 2 x 0.118) or 1.377″. (It is hard to directly measure the inside diameter owing to various reliefs in the metal). This is right in the range of 1.364″ (75-150mm Series E Nikon zoom) through 1.427 (50mm f/2 Nikkor-H) which allowed a straight glue on of the CPU, so glueing the CPU in place such that it’s base (non-contact side) is plane to the inner diameter of the baffle confers the right contact position.
Lens correction profile:
This lens has some chromatic aberration at full aperture and modest vignetting which disappears by f/8. You can download my custom lens correction profile for use with PS or LR by clicking here.