Care needed.
I finally got around to mounting some glossy prints made on the HP paper I received as a gift.
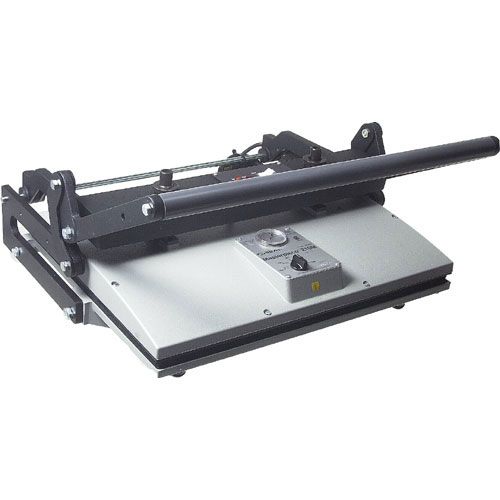
The Seal 160M.
I use a Seal 160M press which I bought ages ago, used, on eBay for some $400 + half my net worth in shipping. It weighs a ton! They are still in business and even shipped me some missing nuts no charge. Today’s price- some $1,400 – reflects the uncompetitive cost of US labor. Will we ever see a flood of cheap ones from China? After all, a press is just a couple of slabs of cast iron and a heater. I doubt it. Few make big prints for mounting any more and I doubt the replacement market in commercial businesses is significant.
Only a fool buys these new. They regularly crop up for $250-500 used and all parts are readily available, not that there’s much to go wrong. The 160M weighs 60 lbs so try to buy locally. The 210M comes in at a whopping 75 lbs. Buy locally and bring a friend.

Typical eBay selling price – this is for the 210M. The 210M has two pressure adjustment knobs in contrast to one for the smaller 160M
The device could not be simpler, so if the heater or thermostat blows, replacement is cheap and the process simple. The whole thing is made up of less than two dozen parts, and B&H carries the essential ones. Framers’ Island also carries spares, including thermostats.
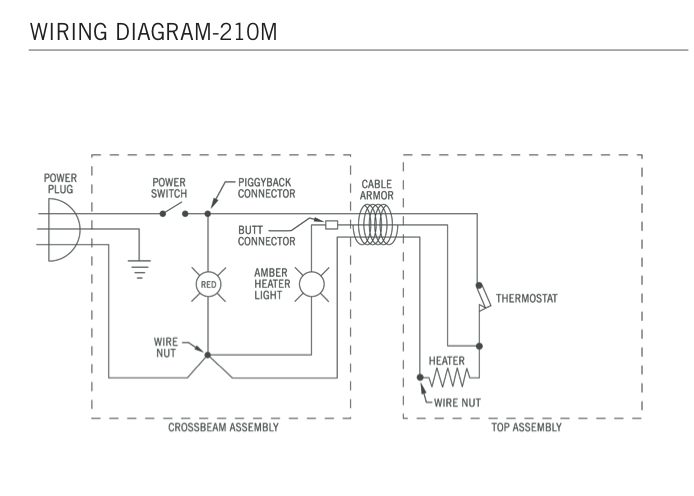
Not exactly complex ….
You can read all about mounting prints here.
I turned the temperature down from my usual 190F (HP Satin) to 170F for the glossy and also first removed the heated platen and gave it a thorough scrubbing with steel wool to remove any surface imperfections. You know how glossy is! Further, I’m careful to keep the release paper (prevents the print sticking to the heated platen) in a dust proof bag to avoid ingress of particulate matter which could mar the surface.
The results are simply spectacular. The surface loses a minor amount of gloss (it will much more at 195F so temperature seems critical) and there’s not a divot or scratch to be seen. But it is a labor of love! The faster these prints go behind glass, the better.
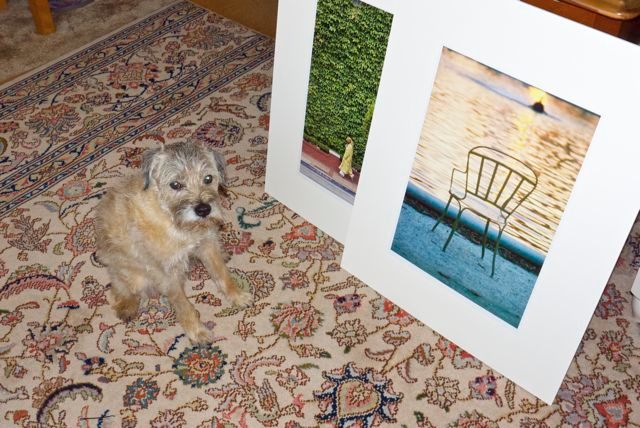
Mounted glossy prints with helper.
To learn more about the Seal press click the download buttons below. If you track down a used one, look for the S or M designation in the model number, indicating it’s a later model which does not use asbestos in the wiring insulation. Life’s too short as it is.

Download the Seal 160M/210M manual. 160M – up to 2×18.5″,
210M up to 2×23″. Both accommodate any length.

Download the Seal 110S manual – up to 2×12″
The maximum width of a board which these will accept is twice the larger dimension of the platen – you simply flip the board around. Overlapping/reheating a previously sealed area has no deleterious effect. The maximum length is infinite as you simply slide the board sequentially through the press. A 13″ x 19″ print needs two passes in my 160M, whereas an 18″ x 24″ requires four, both when centrally mounted on a 22″ x 28″ mat. It’s the size of the mat, not of the print, which constrains capacity. 2 minutes under pressure per ‘press’ using Drymount mounting tissue and release paper does the trick.
Nothing beats a professionally mounted print and, as I have written before, I am still searching for evidence of fading or discoloration in prints I mounted almost 40 years ago using a domestic iron. So when snake oil salesmen come calling, telling you that heat mounted prints fade, ask to see the evidence.