Oh! boy.
If you think the ergonomics of the iPhone as a camera are awful – and they are – you should try the 1950s Exakta Varex.
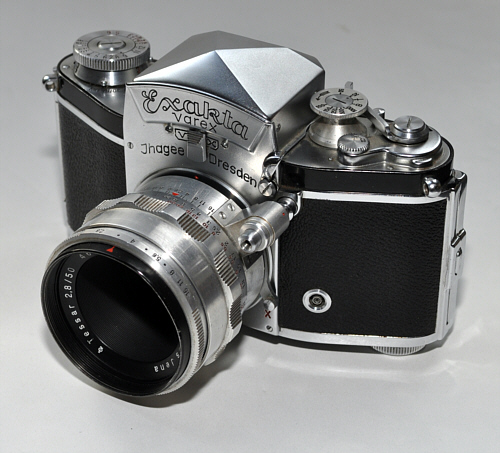
Ergonomic nightmare.
Made in East Germany, which probably says it all, this camera was uniquely bad when it came to hand-held use. The film wind was left handed, though a massive arc with a pencil thin lever which needed two or more hands to operate. Multi-stroking was a no-no. So, naturally, the shutter release was also left handed, and with auto diaphragm lenses the protrusion on front of the lens covered the shutter button on the body. First pressure stopped the lens down, further pressure tripping the shutter. The release button stuck out a mile, making use a challenge. On early lenses the diaphragm had to be manually re-tensioned with a concentric lever on the lens. There was no focusing aid in the dim pentaprism so you sort of sawed the lens back and forth until the image was at its least unsharp. True masochists opted for the waist level finder, which made things even worse.
There are two shutter speed dials, but the main one atop the body can only be set in one direction, counterclockwise, so you may have to hose it around through almost a full circle to get to the next slower speed. Set it to ‘B’ and the secondary dial comes into play, with extended speeds down to 12 seconds. There is no rhyme or reason in the speed settings or progression and you have to separately wind that second dial. Well, you are beginning to get the idea by now. This thing is a disaster.
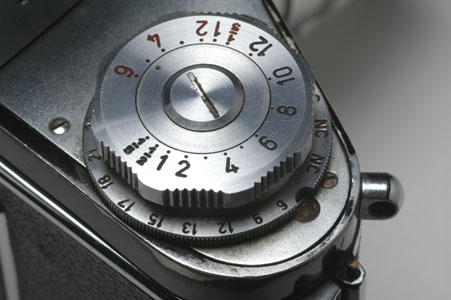
1/5th second? No prob. Choice of two.
The bayonet lens throat was very small, making design of fast and wide lenses a challenge. For reasons known only to themselves, the excellent Swiss Alpa and the no less excellent Japanese Topcon SLRs used the Exakta mount, though both had the sense to opt for a right-handed shutter button. Alpa stuck with external aperture actuation whereas Topcon at least had the sense to internalize the mechanism. Unsurprisingly, both marques failed. A real shame in the case of the Topcon which was extremely reliable and robust, much favored by the US Navy.
However, should you opt for cassette to cassette transport of film in your Varex, there’s a film cutter in the base. Pull it out and your film is sliced in half. So you have that going for you.
The chances that all this wonderful Commie engineering will actually see anything work in this body after all these years – they have a nasty habit of rusting as stainless metals were anathema to Stalin’s forces – are pretty near zero, which is in keeping with the general spirit of this disaster. I recall selling these new (they struggled on with later models through the late 1960s), during my Years in retail and they felt fragile even when brand new. The last version – the VX1000 – added an automatic return mirror, just one more thing to go wrong. Nice to display these for their funky looks, but if you want lousy ergos in a working camera, stick with your iPhone.