Frustrations and fixes.
Background:
Let me warn you that resurrecting an HP DesignJet printer from cold storage makes a date with Sophia Loren a piece of cake by comparison. After the lovely Sophia has turned up two hours late, wants a change of venue and has thrown a shoe or two at you, things go swimmingly well as you gaze into her lovely brown eyes and luxuriate in the prospect of her gorgeous lips on yours. But try resurrecting an HP DJ, by comparison – and it is every bit the exemplar of its caste as Sophia is of hers – and before you know it you will be the one using bad language and generally throwing things in frustration. Having just gone through that process (the HP, that is, not the date with Sophia) you would not be surprised to find some bad language in what follows.
The problems discussed below are by no means unique to the DesignJet. Use a printer as infrequently as I do and you will inevitably run into problems. These devices have many moving parts, some with very tight tolerances (like printhead jets) and occasional use does not help keep things running smoothly. Unlike a monochrome laser printer, color inkjet printers will give you trouble and they will need maintenance.
It’s a couple of years since I wrote about head cleaning for the HP Designjet 30/90/130 wide carriage ink jet dye printers. (A much improved piece, dated April, 2023, appears here). My HP DJ90 is capable of making quite outstanding prints and the Vivera dyes used in the ink cartridges come with an 80+ year life. My latest box of paper from HP says that Wilhelm Research certifies the paper to be fade proof for 82 years when used with HP Vivera inks. So if the print I gave you fades, sue me. I’ll long have been fertilizer.
Here’s an update of my recent experiences with the DJ90 (18″) and everything here should apply likewise to the smaller DJ30 (13″) and the larger DJ130 (24″). This line of printers may have been discontinued for a couple of years now but parts, ink and paper remain available and the small footprint of the machine and its excellent print quality make the effort of maintenance and repair worthwhile. A replacement will be well over $1,000 for the larger variants (a 24″ current model HP starts at $3,500 whereas Amazon still lists new DJ130 models for under $800 delivered – talk of a bargain!) and while the newer machines use allegedly even more fade proof pigment inks (dyes soak into the paper, pigments rest on it, so paper choice is important) you are dealing with a whole new world of hurt when the replacement inevitably fails. And it will.
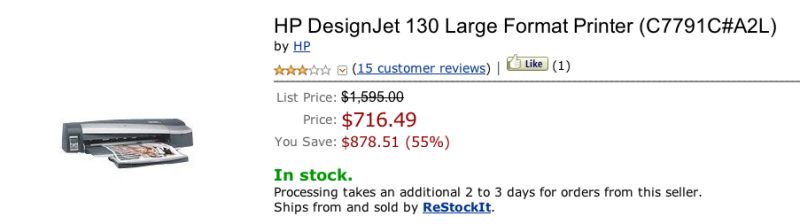
The 24″ DJ130 remains available new – a tremendous bargain.
So for me it’s a case of ‘Better the devil you know’, and have you ever tried moving and installing one of these behemoths? I would stick with the non-roll capable model illustrated above (rolls of paper are a pain to mount, align and uncurl after printing) and the network capable one is a waste of money if you use a Mac as you can network a regular model using just the capabilities of OS X. The poor ratings at Amazon seem largely concentrated on problems with paper rolls. I have had no issues using the front loading paper tray.
Snow Leopard:
Mac OS X Snow Leopard changed the way printer drivers are installed. Instead of coming with a bunch of drivers with the operating system, SL determines the make and model of your printer and goes out to the web to download the appropriate driver. That’s nice, as it means less clutter on your hard drive, but the problem with SL is that it no longer permits the HP Maintenance Utility to work. HP has stated they will not be updating their Utility for SL. However, if you follow the front panel button press sequences illustrated earlier, and repeated below, you can get most of the functionality of that Utility without running any software, which is just as well as the software sucked even when you could get it to load from HP’s crappy servers; the alternative is to run maintenance tasks through Windows but life is too short to go there:

However, there are two snags with HP’s diagnostic and maintenance routines:
- Faulty heads are detected and reported sequentially, one at a time. If you have more than one faulty head, only the first one is reported. Replace it and the next faulty one is reported. And yes, I have homicidal feelings towards the engineer who designed it that way.
- The push button sequence above will not work until all your heads are reported as working properly, so until they are, you cannot run the head flush (‘printhead recovery’ in HP-speak) sequences. Now I’m loading my Dirty Harry Magnum 44, ‘The Most Powerful Handgun Made’, and searching out the SOB who designed it that way.
Paper and ink choice:
The DesignJet uses ink dyes so the paper you use must be capable of absorbing these. Not all papers are absorbent, so either buy HP paper or look for paper which works with HP Inks #58, #72, #84 or #85. The DesignJet uses the last two. Alternatively look for paper which specifies suitability for HP DeskJet 9300 DeskJet 9600, HP Photosmart 8750 or HP DesignJet T1100, T610, 30, 90 or 130.
I always use HP ink cartridges (HP 84 C5016 Black, HP 85: C9425A Cyan, C9426A Magenta, C9427A Yellow, C9428A Light Cyan, C9429A Light Magenta) as I believe the savings from refilled cartridges do not outweigh the risk of using unknown inks. Further, the DesignJet is a very frugal user of ink. There are also aftermarket continuous flow ink systems with high capacity ink tanks for high volume printing but I have no experience of those.
Paper profiles:
Everything you need to know about profiling paper for your DesignJet with Lightroom appears here.
Frankly, your best bet is to use HP Premium Plus Photo Paper – Satin. It’s tested 82 year fade proof and glossy is awful for exhibition use. There are ‘icc’ profiles available from HP specific to this paper and the DesignJet printer. Further, the surface sheen changes little when heat mounted and you know that the inks are being properly absorbed as the paper is made to HP’s specifications. Use something else and you have no certainty of knowing whether the print will fade or not.
HP Support:
Forget about it. It’s useless. Paying for someone who cannot speak English to tell you to reboot your computer is not support. Man up and do it yourself.
Print heads and the cold storage problem:
Leaving the HP Designjet printer unplugged is an extremely bad idea, as my recent experience testifies. The printer was unplugged for a few months while being relocated and when I finally plugged it in, all sorts of problems cropped up. If you switch the printer off but leave it plugged in to the mains the green front panel light will stay on and if you open the ink cartridge drawer cover you will find that the area in the vicinity of the heads is permanently warm. That’s because HP heats the heads even with the printer off to prevent ink drying and clogging. Bottom line is NEVER UNPLUG THE PRINTER FOR ANY PERIOD OF TIME. By all means turn it off with the front panel button but leave it plugged in. The green diode stays on to confirm it’s warming the heads but the fan is off, saving on wear and tear and taking away the noise.
I already knew this but like a fool disregarded that inner voice, (moving is hell), so when I switched it on after a few ‘cold’ months it was hardly a surprise to see the printer reporting a faulty Light Magenta head, evidenced by the blinking symbol on the LCD panel. I get my HP supplies from Atlex and have for years. They have cartridges, heads and the special HP paper for the DJ series, so I ordered a replacement LM head, which was on my doorstep in one day’s time. How they consistently manage this incredibly fast delivery from Illinois to northern California I don’t know but it’s a superb business and you should give them some of yours next time you need HP supplies. They have been around seemingly for ever.
Switching on the printer and opening the head/ink cover, you wait a few seconds while the head assembly moves left then right, open the head cover (toward you, up, away from you) and pull out the old head, pushing in the new. Switch off, fire it up again and ….
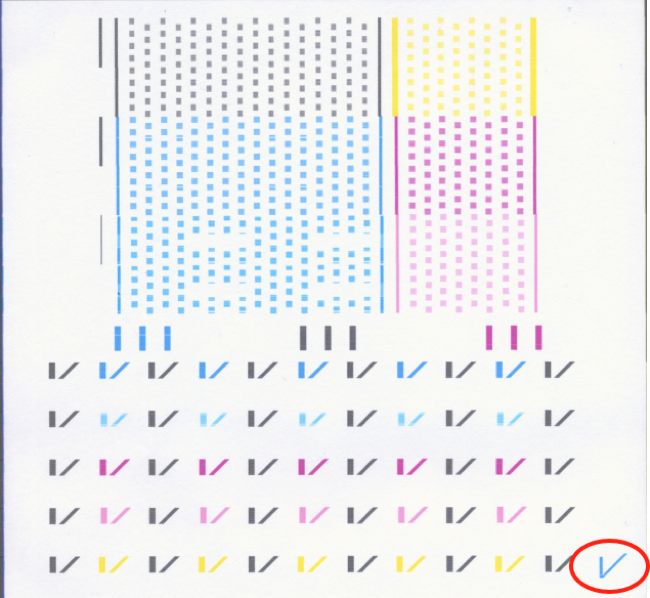
Good head alignment print – note the check mark (circled) lower right.
The Yellow Problem:
For some reason the yellow ink is the one most most prone to clogging the supply tube which routes it from the cartridge to the printhead in the DesignJet. It’s not a printhead problem – the LED panel on the DJ continues to report a perfectly fine yellow printhead yet your diagnostic reports show yellow to be faint or missing. The tube is clogged.
There are two options to fix this.
First, print a dozen or so copies of this file on plain paper in your DesignJet. Load it in any app where you can make it fill the page and set ink use to ‘best’ and/or ‘heavy’. You are simply forcing a lot of yellow ink through that clogged tube to try and clear the coronary thrombosis it’s suffering.
Second, if that fails, replace the ink tube assembly using the below linked supplier and the instructions you will get by clicking the ‘Download’ logo below, which will get you details on how to remove and replace the tube assembly.
Chances are you will end up replacing the tube assembly. It’s some $50.
Wonder about the magenta tint in the reports below? Yup. The Yellow Problem.
Replacing the feed tubes:
Download the Service Manual below and it has excellent and fault free instructions on replacement of feed tubes. I used the supplier mentioned in this article and the replacement came in an official HP box. I downloaded the manual to GoodReader on my iPad and followed along. Links are interactive so jumping to a page is a touch away.
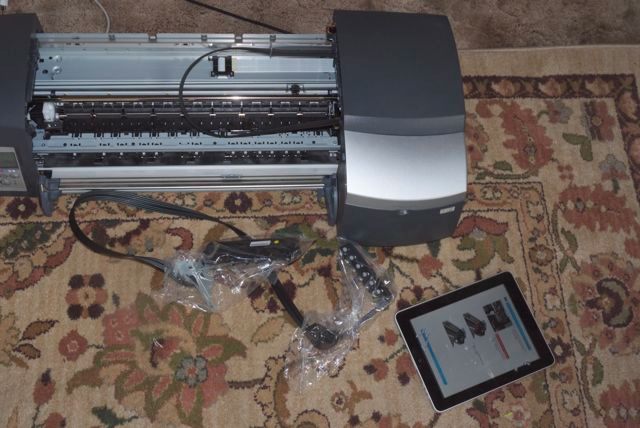
New feed tubes ($50) and the manual on the iPad.
The whole replacement process took me 45 leisurely minutes. The trickiest part is replacing the right hand head cover, but do it just so and nothing will break. Not for klutzes. You will need Torx 8 and 10 screwdrivers and a flat bladed one to help release the catches on the right side cover. Use the wrong type of screwdriver and you will be buying a new printer. The following picture makes everything clear. The yellow feed tube is clogged:
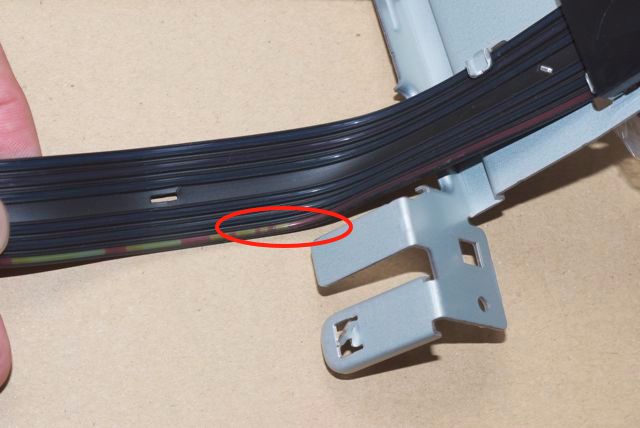
Yellow clogged feed tube is circled in red.
The feed tubes from the ink cartridge to the head are extremely fine so I gave up on any idea of blasting them through with compressed air or cleaners. You can see just how fine in the following snap:
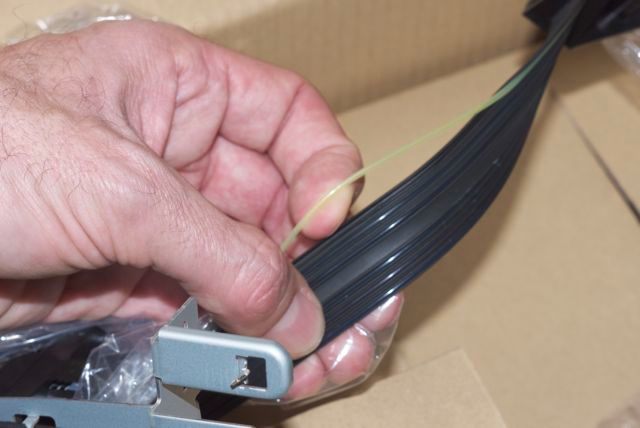
One feed tube – yellow – pulled away from the rubber guide strip.
After doing this you need to prime the new feed tube assembly using the button sequence in the Service Manual. Though the manual says not to prime tubes which have already been primed (meaning the ones in your machine) I did the priming process anyway (not being about to replace six heads) and all went well. Thereafter a quick head alignment and an Image Quality Diagnostic print confirmed that my yellow was back as evidenced by the proper colors of the two large green color squares in the test pattern – compared with the original I made when the printer was new five years ago.
Bizarre patterns on the head alignment report:
One reader of this piece contacted me with a picture of a strange pattern he was getting on the head alignment report. I annotated it and it looks like this:
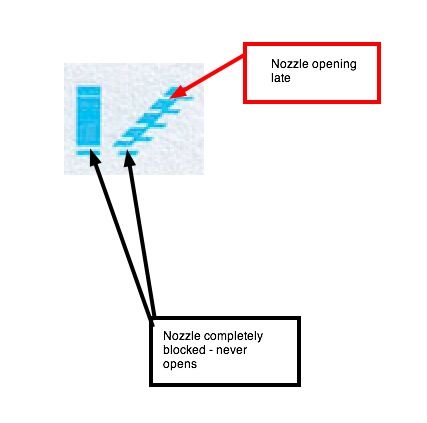
Strange ink pattern from a reader’s DesignJet.
His Image Diagnostics print was OK – some head alignment issues but nothing major – but three of the colors were producing the above pattern on the head alignment print.
After some discussion it transpired that his DesignJet uses a power source subject to occasional brown-outs and power-on spikes. This suggests that three of his heads were fried by an inductive power-on spike and need to be replaced. Head cleaning – soft, medium and hard – made no difference. If you see this on yours, change one affected head first before throwing money at it. With a set of new printheads running some $200 you can solve the math to see whether it makes sense to install a surge protector in your printer’s power feed.
Follow up: It turned out no to be an electrical issue after all. Reprinted below, with permission, is Dave Shankie’s email explaining how he resolved the issue:
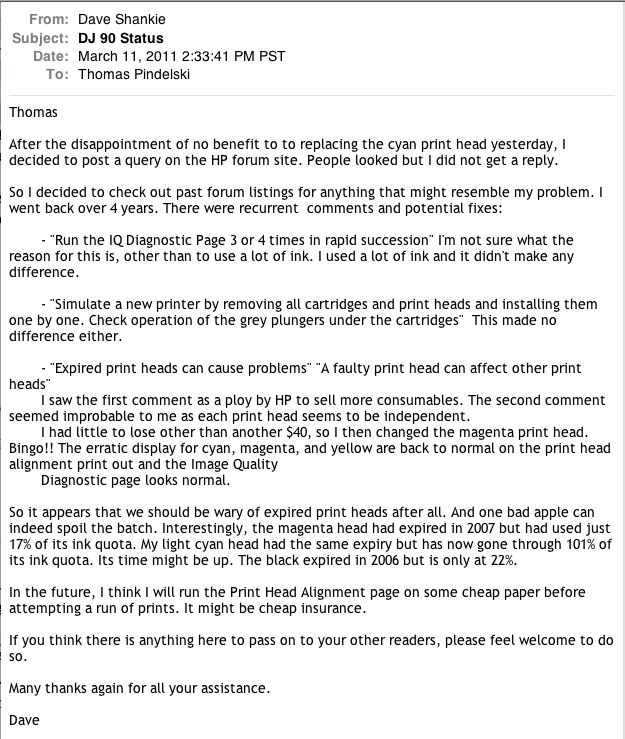
Thanks, Dave – this will help other Designjet users on the recovery trail. The HP site Dave refers to can be found here.
Resuscitating bad heads:
While I have had no joy trying to bring back bad heads to life with water or isopropyl (rubbing) alcohol, whether wiping on the spray ends or by dunking the whole thing, the same reader with the above ‘fried head’ problem (Dave S. from beautiful Vancouver Island) managed to bring a clogged head back to life using more caustic solvents. He first wiped the head with acetone, then with methyl alcohol, followed by a distilled water wipe.
Some warnings are in order. Acetone is nasty stuff. Do not soak a head in acetone – the plastic will melt, destroying the head. Use eye protection. Avoid open flames. Don’t breathe the fumes. Methyl alcohol is not much friendlier. Take the same precautions. Keep the family pet well away. The stuff in your Bloody Mary is ethyl alcohol, so don’t take a shot of the methyl if things don’t work out. Both methyl and ethyl can make you blind if ingested in quantity, but it’s usually a permanent result with methyl.
Printheads have a finite life – something like 3-4 of the large ink cartridges per head (which is a lot of prints) and will eventually need to be replaced. However, Commenter ‘design-jetset’ (see Comments below) managed to salvage his heads whose contacts were oxidized from extended cold storage, using a product named Deoxit, available from Amazon in both the US and UK. Be sure to get the one linked – ‘D5’. There are many variants.
Spare parts:
I’m a big believer in fixing it if possible. HP DesignJet printers are unlike modern digital cameras – it actually makes economic sense to fix them if you do the work yourself. Spare Parts Warehouse lists many replacement parts for the Designjet series (the link is to my base model DJ90, no network card or roller mechanism). I bought my replacement feed tubes from them (see above) and they came in the ‘official’ HP-branded box in short order. They seem to have everything from drive belts to motors, so it’s nice to know a long life awaits my DesignJet.
The feed tube assembly for the DJ90 is part # Q6656-60103; for the DJ130 it is # Q1292-60235 – use these numbers to search for replacement parts in your browser. Amazingly Amazon lists both as of March, 2015 – $166 for the (rarer) 90, $65 for the 130. I have not tried it but would bet that the 130 part can simply be cut down to fit the 90 – the end fittings at the printhead and ink cartridge ends are identical.
Reports:
The following reports were run before replacing the feed tubes to cure the clogged yellow one, hence the magenta cast, clearly visible on my profiled display. After feed tube replacement they print in solid, neutral black, as they should.
The usage report (see above for button sequence) for my DJ90 reports a modest 460 print jobs (HP cannot add properly – see below) so I expect many more years of life from the behemoth.
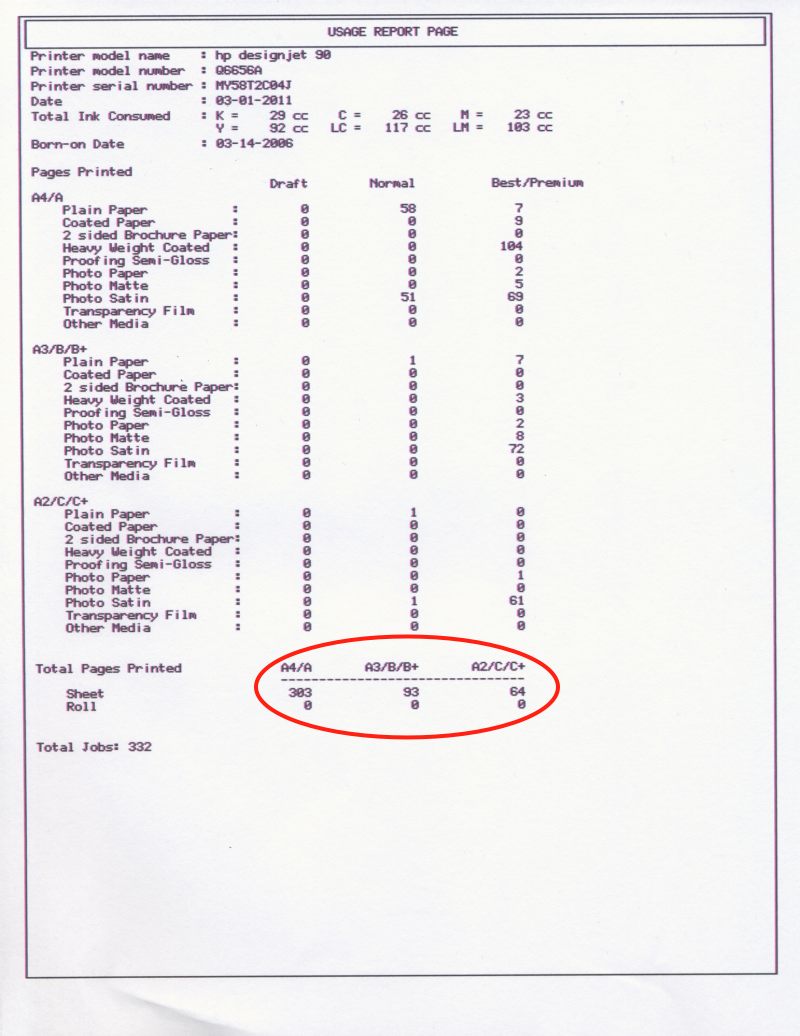
Use report. Holding the Power button press the ‘OK’ button once to generate this.
To get the more detailed Information report, holding ‘Power’ press ‘OK’ four times; here’s an extract of the two page report:
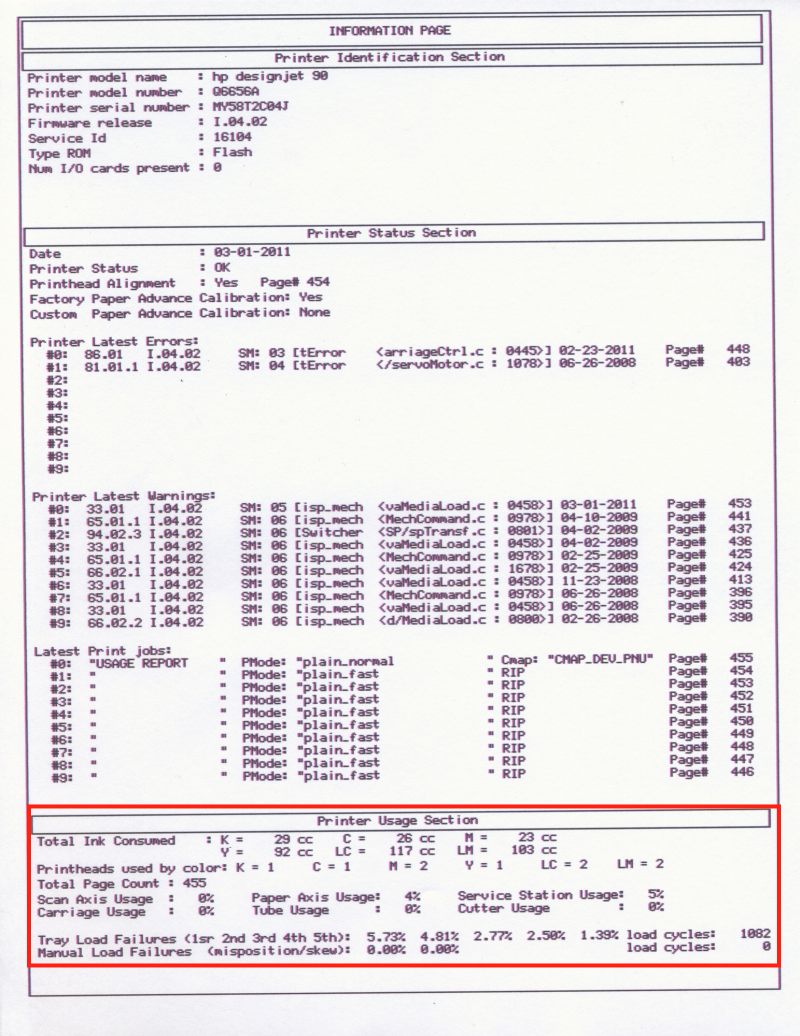
Information Report, Page 2.
If you are contemplating buying a used HP DJ 30/90/130:
A good, used DJ90/130 is one of the cheapest ways of getting large format, high quality printing.
Don’t pay more than $350 for a used DJ90 or more than $500 for a used DJ130 and only buy ones which can run the above report – which means that all the printheads are functioning as you cannot run the report otherwise. Don’t buy one where the seller claims he cannot run the report because ‘….one of the ink tanks is empty.’ Move on to the next one. Try and buy locally to save the beating UPS will give it. Inkjet printers are not robust devices.
The above report will tell you whether the machine is a pro’s beater (many DJs were used in print shops and you really want to avoid those) or an amateur user, like mine. Note in the red box, above, you can even see how many times the print heads have been replaced! A high count here is a sure indicator of heavy use or recurring problems – avoid. I’m not sure of the meaning of ‘Service Station Usage – 5%’ in the above but suspect it refers to the area where ink overflow from the cartridges is dumped. If I am right then you can see my DJ90 has had a very easy life indeed.
I suspect a used DJ30 (13″) is a waste of money as a new printer with that modest size capacity can be had inexpensively.
Printing over a network:
You do not need the network version of this printer if you use Mac OS X. All you need is an Airport Extreme or Airport Express wireless router, or a lot of time to mess about with aftermarket routers. The Apple products, when used with a Mac, are truly ‘plug-and-play’.
In its previous location my DJ90 was hard wired to my Mac with a USB cable. No more.
My workhorse HackPro, whence I print, resides in the home office and gets its network connection wirelessly from a remote Airport Extreme router in another room; the HP DesignJet 90 is connected to that Airport Extreme, using an USB cable and added to the list of available printers in System Preferences->Print & Fax.

No need to check the network sharing box with Bonjour.
Printing wirelessly from the HackPro is easy as can be. You don’t need high speed networks for this sort of thing as the printer is the slowest link in the chain and it is slow compared to any other peripheral you may have attached. Plus, OS X buffers the print job to disk if you use PS or LR so the application need not even be running once the print job is spooled out. I mention this as Apple’s Bonjour wireless technology which is being used here was a complete dog in the early versions of OS X but is now seamless and trouble free. Back then it was named ‘Rendezvous’ which is about as inaccurate as it gets.
You can even print to an HP DesignJet connected to an Apple router from your iPad or iPhone if you use an app like FingerPrint!
Well, the DJ90 is back in action …. until the next time.
Error codes:
The DesignJet has extensive error code diagnostics – here are the error codes if you need to repair yours; you can see some error codes (paper jams) in the report above:
Image Quality Diagnostic Page and Color Calibration:
Now here’s the real snag.
You can only print the Image Quality Diagnostic Page (see my earlier piece for an example) and recalibrate the printer for the latest HP paper using Leopard or earlier if you are on a Mac. That’s because Snow Leopard and later Mac OSs will not allow you to run the System Maintenance Utility. So either borrow a Windows computer (no files are transferred – the printer stores everything you do), use a Windows emulator like Virtual Box or Parallels or do as I do, use an older Mac running Leopard or Tiger. I use our old PPC G4 iMac running Leopard 10.5.8 and it works fine. You can still download the System Maintenance Utility from HP’s web site.
Finally, for the really serious:

Click to download the HP DesignJet Service Manual brochure.
This is the official service manual and if it’s not in here it probably does not exist. The software section is Windows-centric, wouldn’t you know it, but there are complete dismantling and replacement instructions toward the back which should ensure your DesignJet has the longest possible life! The file is some 8.9mB in size, so it will take a while to download. All versions of the DesignJet 10, 20, 30, 50, 70, 90, 100, 110, 120 and 130 are covered.
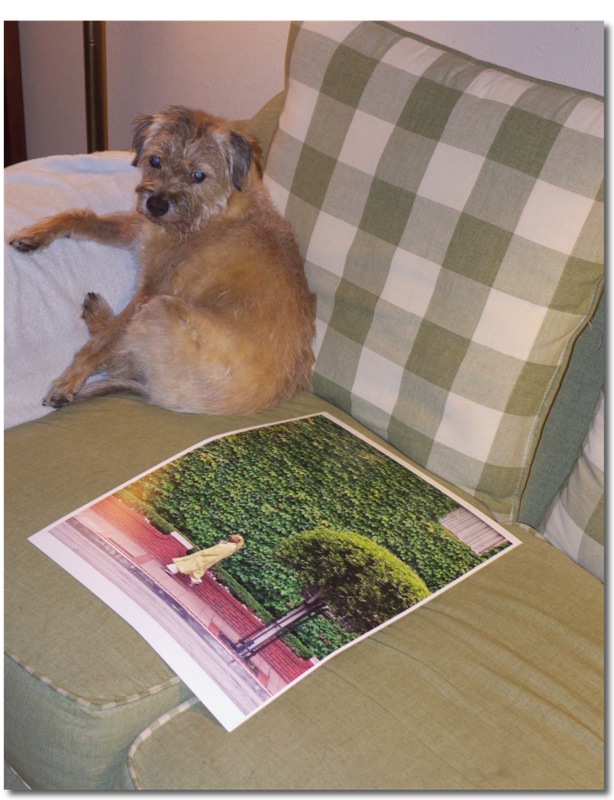
Finally, a big print.
To start with my situation: I bought a Designjet 90 cheap (not working of course) as my first larger format printer, for my first attempt at selling my work. Replaced the heads first, everyone of them was clogged …. it wouldn’t print a thing.
On to your blog; thank you so much!!! So informative, so in depth, and written to be understood by all. I saw the blockage in my yellow tube right before I found your blog. Also the link to the service manual is awesome! I’ve been googling the heck out of yellow ink issues with the designjet 90 for hours…and you had the problem listed as a known issue. No I haven’t repaired it yet, but the thanks is in advance.
Sincerely, Thanks again for the information and all the other tips relating to the designjet line.
Kevin A Moore Seattle, WA
Thomas…you’re awesome for posting all this info and including the helpful links! I was leaving my DJ unplugged (for fear that our frustratingly frequent city power outages would fry the power unit) and didn’t even think/know about how it affected the ink.
Here’s a tip for you…buy HP inks on ebay and you’ll save around 50% of what you’d pay at Atlex!
Best Regards.
Carmen – Thanks for the kind words. However, I do not agree with your suggestion to buy inks on eBay. eBay is the repository of more crooks than are in our prison system. Many of these cartridges are outdated and will not work (the DJ checks age on the cartridge’s chip). Other have been illicitly refilled with aftermarket inks which variously destroy the printer or fade rapidly once the print is made. Saving on cartridges is the ultimate false economy if you care about the longevity of your printer and prints.
As regards the power outages, simply get a small surge suppressor and install it between printer and power. $20. Then leave the printer plugged in (but switched off) at all times.
You are a life saver – well, okay, not actually, but certainly a SANITY saver. I, too, am an amateur who LOVES my D90R, except when I HATE it! It does go from perfect to dysfunctional in a heartbeat. I have learned to stockpile one each of the printheads. Your tips for fixing the thing have come in handy on a number of occasions. Thank you, thank you!
I wonder what your experience has been with the “new, improved, fast drying” HP Premium Plus Satin paper. It has been the only paper I have used for photo projects for years, but I am distraught with the new version. The color does not match my screen (tends to green) and fades within months. I tried in vain to talk with HP-no-English-support and that was just an exercise in futility. I quickly ordered a couple of rolls of the 18 x 50″ paper, as this does not seem to be “new and improved” yet. Do you have any alternatives for letter size paper to recommend?
I have switched to HP Glossy so I’m afraid I have no experience of the new HP Satin. – Ed.
You mention that after installing the yellow tube that you went through the priming sequence. Can you please tell me what that is. I’ve had printhead problems with my hp 130 since it came out of the box. I have no less than 10 printheads which are probably fine but hp has replaced to shut me up. Each time that was their fix. 20 days prior to warranty expiration they finally sent out a service tech. Who was great, but, 30 days after his visit the machine started the same mess. Guess what, now without payment they won’t help because my machine is out of warranty. Sorriest bunch of thugs I’ve ever dealt with. After writing to the chairman of the board for hp they did call me and tell me that the service tech must have forgotten to prime the machine—which I don’t believe, because the machine worked fine for 30 days. Anyhooo, hp had me go through a series of head standing, cord unplugging while at the same time pushing button process. By which you needed to be a 3 handed person with contortionistic tendancies to manover. At any rate—it worked and my machine has functioned perfectly since up til about 3 weeks ago. I suspect the machine has lost it’s prime as I am a low volume user. I think that may be the problem with the yellow is that is has a tendancy to loose it’s prime more easily. Don’t know, I’m obviously not as versed as you on these little monsters but, could you please put up the button pushing recipe for priming. Best Regards, Ginger, AR
Ginger –
I leave mine plugged in (which keeps the head warmer on) and do not need to prime even after months of non-use.
Download the service manual linked here. Go to pages 4-2 and 4-8.
Keep the manual – it’s well written and invaluable for, as you have already confirmed, the worst run Fortune 100 company with its annual CEO changes sure as hell is not going to help you. This was a great comnpany when I was a Mech Eng student (UC London, class of ’73) but of course some jerk-off sold the one great thing they had going – their measurement and instrumentation business.
Mercifully all parts remain easily available – the links you need are here. The worst case may be you have clogged feed tubes or bad heads. But you should only need to prime new feed lines once.
– Ed.
I just wanted to say thank you for taking the time to write this blog post and document the process. My HP 130 was in enforced cold storage (I really had no choice) and of course threw the largest fit when I turned it back on. Thanks to your post and the brilliant manual I identified the problem, found parts and repaired it. Now it’s running well and happily ensconced in it’s new position and will not get turned off.
Best wishes Rosie
Thanks for this blog, it’s very helpfull. After six years of just having problems with printheads (replaced and solved) I’ve jus arrive to the yellow tube problem (after trying to solve it, now is yellow and cyan problem cause I used a very old and wasted cyan cartridge to purge. I think it has more to do with a loss of watertightness than with a clog that is the next consecuence. Why, and specially where is originated, and why can’t be easily solved with a purge, which by the way, didn’t make any mess in my hp 130, is what I’m investigating now before spending my last 50 euros in a new tubes assembly. Any suggestions ? I’ll keep informed but dont know if it’s worth, cause new hp 111 are now very, very cheap About 580 € and come with a complete set of 4 cartridges and printheads that are 320 € in consumables.
Thanks again.
http://www.delex.es/plotters-hp-designjet/hp-designjet-111.html?gclid=CLiS94DjobQCFYXLtAodrVUAIQ
Guillermo – A couple of thoughts. The HP30/90/130 are 6 color dye printers, need compatible paper which is getting harder to find, and deliver the best blacks in the business. The HP111 is a 4 color pigment printer (the colors dry on the surface rather than being absorbed by the paper), can use a far broader range of papers which are easy to find but you really want to see some prints before you spend $1,000 on one. Just because the consumables are included does not make the HP111 a good buy. The way I see it you can find out if your DJ130 still works for 50 € or spend 580 € on an unknown quantity. The results I have seen from the latest 12 ink Epsons are no better than those from my DJ90. I have not seen output from the HP111 so cannot comment.
I also have serious concerns about HP as a business. It has to be the worst managed large company in the world. One day they are getting out of printers and PCs, the next day they have a new CEO, the third day they are litigating to cover up for their mistakes. It’s a rudderless ship, too late to mobile, stuck in low margin commoditized and dying businesses (PCs and printers), they have completely missed the tablet revolution, etc. It’s hard to see this company surviving and it has meanwhile garnered a reputation for some of the worst customer service on the planet. I speak from personal experience. There is no scenario on earth where I would call HP for help with anything nor would I buy anything from HP again. Once my DJ90 becomes uneconomical to fix I’ll be getting the latest Epson.
Take a good hard look at the official HP Maintenance Manual to which I link above. It is exceptionally good and has very detailed diagnostics which might help get your DJ130 fully functional again. What do you have to lose?
Along with everyone else that has taken the time to write, I am grateful for your time to write and maintain this blog. I love my DJ130. I’ve been using it for architectural drawings since 2005 when I started by own business. It has rarely failed me, but after a rough cross country move from New England my printing baby has shown up worse for wear. Downloading the manual was a treat as now I have available the tools to allow some DIY repair. My issue right now is ink delivery. To make matters worse, the “Services” tab within the Printing Preferences menu has grayed out the “Status of my Printer” and “Calibrate Color” tabs. Into the manual I go…….
Hello everybody,
thank you very much for this article, I would like to share my experience with you .
I have demounted whole tube system like in this article is described, but I did not order the new one (money, time, impatience) but I have rinsed it by water with syringe.
The old ink was hard like stone at many places so just pressure of water from the syringe was not enought.
So i pulled out yellow transparenttube from rubber cover and massage of hardened places while overpressure and underpressure of water helped. All hardened places were realesed in 30 seconds. Then I rinsed whole system by water and printer goes again well.
This is all really interesting but I’m still trying to figure how to get my DJ90 apart. Mainly the right side, cover and sides etc. I’m pretty good mechanically but not brave enough to go where I’ve never been at the cost of breaking something. so if you could tell me how to access the ink and driver right side so that I can remove the ink tubes I would be most appreciative.
Thanks.
Download the factory manual referenced at the end of this article. It includes step-by-step dismantling instructions. See page 7-5 and following. – Ed.
I spoke with HP tech support today. While they’re still working on the maintenance utility for OS X 10.8 Mountain Lion, the utility for 10.7 works fine for Mac. This is very encouraging Doug, thank you. But frankly, this is HP, so I’ll believe it when I see it on OS 10.8. – Ed.
For some time now I’ve suffered from magenta banding and for a short time, fuzzy printing and I have since solved both problems. I have a Designjet 130nr (don’t use the roll-feed–it’s still new in the box)
The HP Designjet 130 suffered from
1. fuzzy printing which I assumed was a problem with print head alignment.
2. magenta showing in place of gray which I assumed was some color not properly flowing to the paper.
3. late in the process of working to correct the above, I began to hear a LOUD ratcheting sound.
The fuzzy printing was solved simply by setting a print preference in the printer palette, unchecking ColorSync and checking Vendor Matching. I get a finer set of lines without the blurring.
The magenta problem was in the light cyan printhead or the LC print cartridge. I replaced both. No problem with plugged tubes, thank Zeus. I now can print the same quality of gray that I’ve had in the past.
When I start up, the head moves back and forth a bit and the ratchet sound starts. I simply press the (red) cancel button and it resets and allows me to print my sheets. Note I print one at a time off of the big extension table on the front–not from the intake table below the main table. I think the ratchet problem is the machine trying to pick up paper from the lower table. I have 8-1/2 x 11 there (which, it dawns on me, I should remove). I also get, on my large sheets (18 x 24) three small incisor-like marks 2/3rds of the way through my print cycle. Weird.
Bottom line, I can live with the ratchet sound, if I can save 5 bills or more. I’ll look closer at the DesignJet manual when I get a little more free time to get a better idea of the source. The “5 bills” reference was for a repair quote that included an HP kit. I’m wondering if the kit includes all new print heads and inks. Since I’ve already replaced many of these, paying for replacing them again is troubling. The repair people, smelling a Do It Yourselfer, haven’t returned my phone calls.
Lastly, I had a newer ink cartridge which showed ink on the readout begin to not provide ink. I simply let it soak for a few minutes in a mug of hot water and it began working just fine after I’d wiped it down and reinserted it.
I wonder whether the incisor marks are being caused by the built in cutting knife. It might make sense to try disabling it. – Ed.
Thomas,
Thank you for blogging about these DesignJets. I had left my old DJ 130 unused in an attic for more than a year… dusty, sad looking, a mouse had even lived inside it for a while! I cleaned it up and printed a test page, and was surprised to see that all the heads worked perfectly. – For a while… then Yellow stopped printing. Readers of this blog of course know why: the yellow tube was clogged.
I took it apart and followed the method explained by Hanzzz above. I inserted a syringe (from an ink refill kit for a different printer) in the end where the print head is fed, and managed to “massage” the clots in the tube while injecting hot water. I also injected water from the other end (after disconnecting the Cartridge end of the tube). The clots dissolved completely and the tube was 100% clean after a few syringefulls of water.
Finally, I used the syringe to suck some yellow ink out of an old cartridge, which I then used to fill up the tube (i.e. priming it) before assembling everything. Worked first time, prints beautifully!
Here is a tip for dealing with electrical problems with the print heads (indicated by flashing printhead on the LCD display). This is caused by oxidized contacts on the printhead and in the printer itself. To fix it, spray a tiny amount of Deoxit D5 on a Q-tip, and wipe the contacts on the print head (and the mating contacts in the print head station). You can buy “Deoxit D5” on Amazon, eBay, etc. – It is a little expensive but 100% effective with this annoying problem.
Thomas,
A quick tip regarding installing USB drivers for these printers in Windows 7:
If you download the setup program “HP Designjet 130 Series PCL3GUI Installer” and run it on Windows 7, you will find that in fact this setup program doesn’t install the USB drivers properly – i.e. it fails miserably to install, doesn’t even find the printer and ends up stuck, unable to complete the job.
A simple workaround to this is to buy a JetDirect network card on eBay for around $10 – $15 used, and connect the printer over the network. That works fine, and the HP software installs and works.
However it is in fact possible to install the USB drivers on Windows 7 – but you do need to jump through a few hoops. The problem is that the driver file from HP doesn’t correctly map to the hardware ID that the DesignJet reports, so the setup program will never work.
However, HP does offers a separate, smaller Driver file on their web site, called “HP Designjet 30 and 130 PCL3GUI Driver” which can be modified to work.
1. Download the driver file above from the HP web site. Extract the contents into a folder.
2. Plug the printer into a USB port. Do a Properties on the printer in Device Manager, identify the “Hardware ID”
3. Going back to your downloaded driver, open the file dsgj110.inf and change the line that mentions your printer so it now contains the correct hardware ID reported by the printer. For example,
“HP Designjet 130nr”= DJ130,USBPRINT\Hewlett-Packardhp_de490D
4. Now simply install the driver using the standard Windows “Update Driver” function (Device Manager, Properties). Windows now finds the driver and installs flawlessly!
The HP system maintenance tool called “HP Designjet 30 and 130 System Maintenance Utility” seems to have no issues installing on Win 7 64 bit, and works great once the USB driver above has been installed.
Happy printing!
HP 130 C7791C
Mac, connected via USB
I ran a printhead alignment from the front panel (Power+ Cancel 0x, OK3x). It showed no black or lt cyan (or cyan I’m not sure) and I have run the alignment several times with just the faintest bit of improvement. I’m now getting just a little bit of ink from the black and cyan, but I’m nowhere close to good. I’d like to run the Printhead recovery functions – but – the printer is “stuck” in Printhead Alignment mode. When I turn it off and back on it requests paper and then runs the alignment again.
It seem like it does not want to do anything until the alignment test is good. Is there a way to get out of this cycle? I’d like to run the printhead recoveries, see if I can get ink flowing, before I spend on new heads, cartridge or tube assembly.
Thanks Thomas for this awesome forum – thank you to everyone else for sharing your discoveries and knowledge.
-William
Your printheads and/or feed tubes are clogged. Do the simple thing first. Pull one of the bad printheads, wipe it in acetone (careful! Do not soak it in acetone – the plastic will melt) then flush with tap water. Retry. If that fails, access the feed tubes and check for clogs – flush or replace. – Ed.